포스코 동반성장지원단 만나 혁신시스템 접목
‘대·중소 상생형 스마트공장 사업’은 중소벤처기업부가 대기업 등과 협업해 민간 차원의 자발적인 스마트공장 구축을 지원하는 사업이다. 중소기업중앙회는 삼성, 포스코, LH 등과 함께 중소기업의 제조혁신을 지원하고 있다. 중소기업뉴스는 4회에 걸쳐 스마트공장 구축 우수기업 사례를 소개한다.
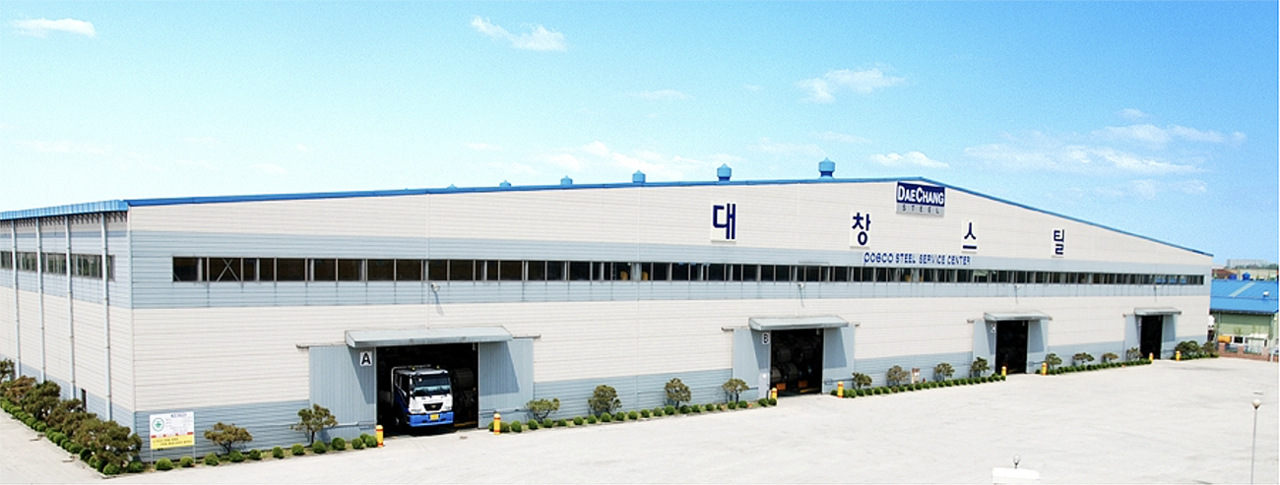
1980년 설립된 ㈜대창스틸은 포스코의 냉·열연 철강제품 지정판매점(Steel Service Center)이다. 포스코에서 생산된 냉연 및 열연 강판을 고객사가 원하는 규격으로 가공해 공급하고 있다.
대창스틸은 기존에도 생산관리시스템(SMIS)을 활용해 영업관리, 생산지시, 생산실적, 재고관리를 하고 있었다. 하지만 공장현장의 원료, 재공품, 제품의 입고, 공정투입, 출하의 소재 이동지시가 수작업으로 처리돼 재고위치가 제대로 관리되지 않았고, 악성재고 증가에 따른 관리비용 증가는 물론, 다른 소재 오투입으로 인한 생산 로스와 이에 따른 고객클레임 발생으로 어려움을 겪고 있었다.
변화가 필요한 시점이었다. 문제를 해결하기 위해 먼저 포스코의 중소기업 컨설팅 전담조직인 동반성장지원단에 지원을 요청해 야드 자동화를 통한 소재·제품 관리 개선을 최우선 과제로 도출했다. 하지만 이를 위해서는 적지 않은 자본의 투입이 필요했다. 고심하던 문경석 대표는 동반성장지원단으로부터 포스코가 지원하는 상생형 스마트공장 지원사업을 소개받고 세 개의 공장 중 먼저 충남 아산공장에 스마트공장 도입을 결심했다. 스마트공장 도입을 통해 원소재 입고부터 출고까지의 물류 시스템을 개선하면 생산효율성 증가로 이어질 수 있다는 판단이었다.
ICT 기반한 입출고 공정 구축
재고 최소화·생산성 향상 실현
조직문화 개선에도 긍정 영향
스마트공장 도입 효과는 놀라웠다. ICT 기반 입출고 창고관리 시스템이 구축돼 창고의 적재상황과 물류흐름이 실시간으로 관리됐다. 입측 크레인에 부착된 IoT센서는 측정된 크레인 이동값을 창고관리 시스템과 연계해 자동화된 야드관리를 가능하게 만들었다. 이와 함께 소재 및 재고의 실시간 상세위치를 관리하는 소재 Tracking 자동화 구현으로 재고 최소화와 생산성 향상도 달성할 수 있었다.
실제로 스마트공장 도입이후 대창스틸의 리드타임은 19% 개선됐고, 납기단축은 57% 단축됐다. 무엇보다 제로(0)의 공정 불량률은 스마트공장 도입으로 대창스틸이 이룬 가장 놀라운 성과였다.
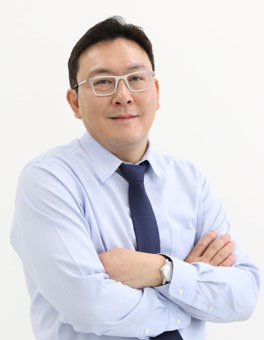
문경석 대표는 “스마트공장 도입은 많은 비용이 수반되기 때문에 중소기업 입장에서는 도입을 망설일 수밖에 없다”면서, “대창스틸도 결정과 시작은 어려웠지만 도입 이후 제품 불량률이 감소하고, 원활한 재고관리와 납기단축으로 고객사와도 더욱 우호적인 신뢰관계를 맺게 됐다”고 밝혔다.
이와 함께 “기존 방식에만 익숙했던 직원들이 스마트화에 익숙해지는 일련의 과정들을 보며 스마트공장 도입이 업무 외 조직문화 개선에도 긍정적인 영향을 끼쳤다는 것을 알게 됐다”며, “가능한 많은 중소기업이 스마트공장을 도입해서 대창스틸 외에도 더욱 다양한 성공사례들이 나올 수 있기를 바란다”고 덧붙였다.