동아플레이팅은 어떻게 스마트공장으로 혁신했나
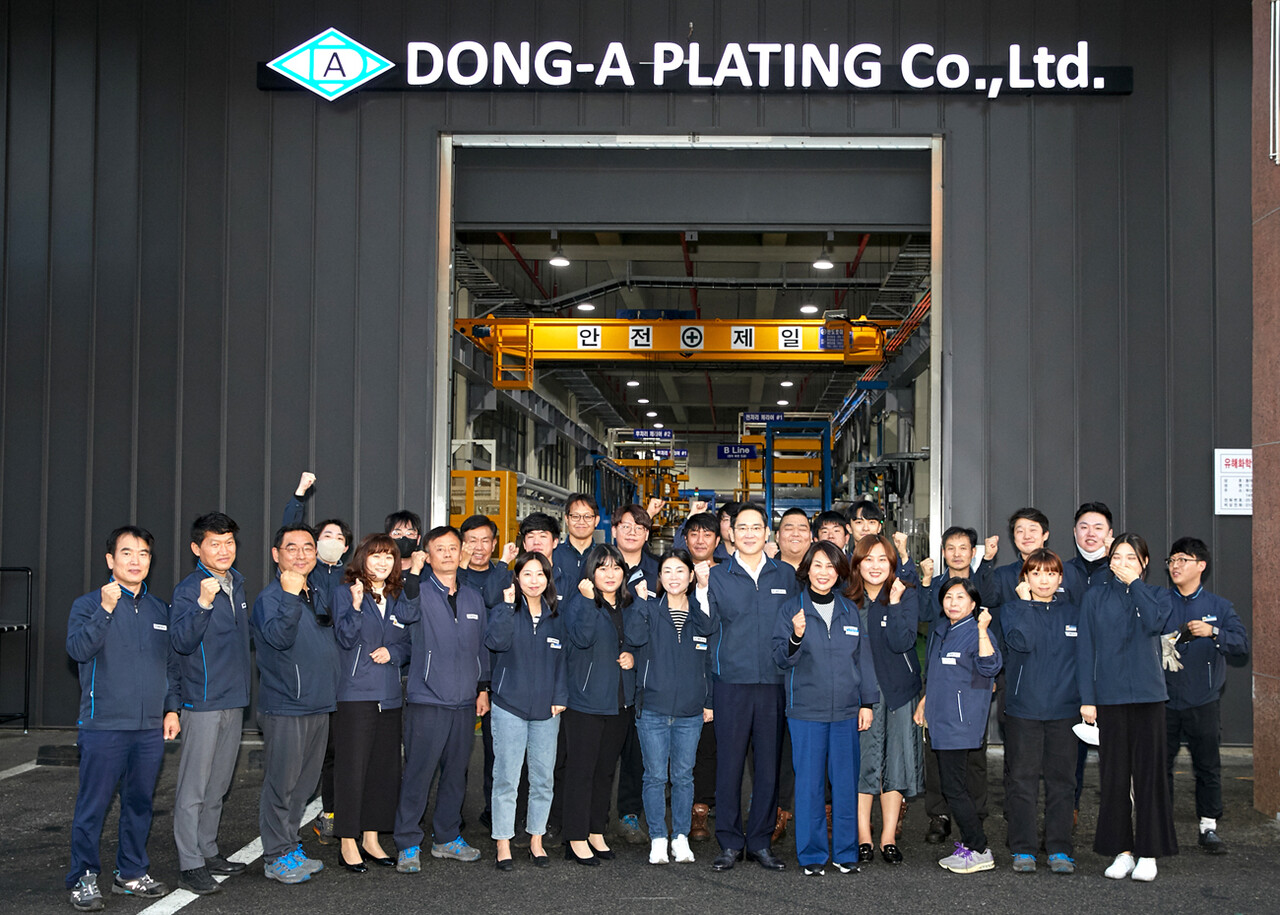
부산에서 자동차 안전부품을 생산하고 있는 동아플레이팅은 지난 2015년에 ERP 시스템을 도입했다. 하지만 현장관리와 세밀한 생산관리에 한계를 느껴서 생산관리시스템(MES)의 필요성을 느꼈다.
철로 만들어진 자동차 정밀 부품의 부식은 사고로 이어질 수 있는 위험한 상황을 야기하기 때문에 정확하고 일정한 품질 수준을 유지해야 한다.
하지만 제품 불량이 발생했을 때 생산이력 확인이 어려워 해결책을 찾기가 쉽지 않았다.
도금 공정 자체가 수작업으로 진행됐고, 거래명세서나 제품출하증 같은 서류도 수기로 작성하고 있었기 때문이다. 때마침 중소기업중앙회와 삼성전자가 공동으로 추진 중인 ‘스마트공장 구축 지원 사업’의 대상기업으로 선정돼 MES 시스템을 고도화할 수 있었다.
삼성전자 스마트공장지원센터의 멘토들은 동아플레이팅에 최적화된 MES 시스템을 적용했다. 멘토링에 나선 김진소 삼성전자 멘토는 “초창기 가장 큰 문제점은 작업 공정에 대한 소요 시간이나 데이터 부족으로 인해 생산계획이 주먹구구식이었다는 점”이었다며 “정확한 생산계획의 수립 없이는 스마트공장 고도화를 이루기가 어렵다는 판단이 섰다”고 당시를 회상했다.
삼성 손잡고 MES시스템 고도화
생산량 확대·시간당 효율 제고
납기 준수·장비수명도 극대화
직원들 안전·행복이 최종 목표
동아플레이팅이 취급하는 제품은 크기와 형상이 모두 다르다. 그에 따라 전류나 전압 등 공정 조건도 다르기 때문에 그때그때 주문에 따라 부품을 생산하면 손실이 발생하기 쉬운 구조였다.
이에 지원사업 멘토와 협의해 제품의 성격과 규격이 비슷한 종류끼리 묶어, 전류와 전압이 같은 것끼리 생산할 수 있도록 ‘배럴 최적화 시스템’을 구축하게 됐다. 그 결과, 기존 8배럴의 생산량이 12~13배럴까지 가능해졌다. 시간당 생산량도 35% 넘게 증가했다.
또한, 공정상의 낭비와 비효율적인 요소까지 줄일 수 있었다. 완제품의 적재 받침대를 개선해 제품 교체 시간이 1일 105초에서 35초로 단축됐다. 수기로 작성하던 작업일보도 전산화하면서 불필요한 문서 작성도 없앴다.
또 실시간 생산되는 정보는 물론 설비의 이상 여부를 모니터링하기 때문에 고장 발생을 예방할 수 있어 안정적으로 납기를 준수하고, 장비 수명을 극대화할 수 있게 됐다. 스마트공장을 구축하며 제품 수주부터 생산까지의 모든 프로세스가 전산화된다. 도금의 품질을 좌우하는 조건들을 실시간 수집하고 분석할 수 있게 된 것이다.
스마트공장으로 전환하면서 생산성도 증가했지만 안전사고까지 예방하는 성과를 거둘 수 있었다. 여기에는 생산성이나 매출보다 중요한 것은 직원들이 안전과 행복이 더 중요하다는 이오선 대표의 철학이 있었기에 가능했다.
이 대표는 “다양한 교육 프로그램과 역량 강화 제도, 직원들의 복지와 근무 환경 개선에 적극적으로 투자해 행복하고 안전한 일자리를 만들어가는 것이 최종 목표”라고 밝혔다.
한편 최근 정부가 스마트공장 예산을 올해 3089억원에서 내년 2032억원으로 1057억원이나 대폭삭감한 예산안을 국회에 제출했다.
이에 대해 중소기업계는 “정부의 예산 삭감안은 정책지원 대상인 수많은 제조 중소기업과 스마트공장 솔루션 및 자동화 설비를 공급하는 중소 공급기업에 막대한 피해를 줄 것으로 예상된다”며 “기업 규모가 작을수록 스마트공장 구축사업 지원은 중소기업의 경쟁력 강화에 필수적인 정책으로 입증돼 왔다”고 역설했다.
스마트제조혁신추진단이 최근 발표한 자료에 따르면 스마트공장 도입 후 경영개선 성과를 분석한 결과 도입 기업의 매출액은 평균 7.7%가 늘어났으며 산업재해감소는 무려 -18.3%에 달했다. 고용증가도 3%나 증가했다.